El Test Center Energy inaugurado esta semana por Seat es el primer centro de pruebas de baterías del sur de Europa. Hemos podido visitarlo y conocer qué tipo de desarrollos y tests se realizan en este pionero edificio. Un complejo de 1.500 metros cuadrados en el que se han invertido más de 7 millones de euros y donde se prueban los módulos de celdas y las baterías para coches eléctricos e híbridos enchufables.
Las baterías son el componente clave de un coche eléctrico, que muchos ya simplifican como "un ordenador pegado a una batería y cuatro ruedas". Pero el proceso de construcción y testeo de una batería es mucho más complejo. Aquí os contamos qué pasos son necesarios para su fabricación y qué tipo de pruebas se realizan en un centro como el construido por Seat en Martorell, Barcelona.
Así es el interior de las baterías de coches eléctricos
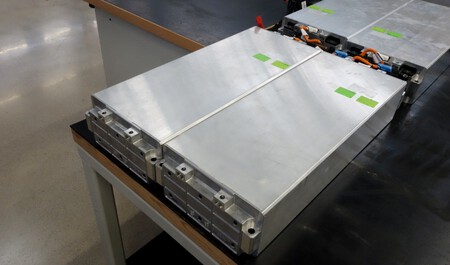
España es el cuarto país donde el Grupo Volkswagen decide construir un centro de pruebas de baterías. Fuera de Alemania, el fabricante dispone de un centro similar en China y en Estados Unidos. Según explican desde Seat, el abierto en nuestro país es más grande que el estadounidense. Este Test Center Energy (TCE) es un centro de pruebas, pero no se fabrican aquí las baterías. Todavía está pendiente de confirmación donde se ubicará la gigafactoría de baterías de Volkswagen en España.
El primer paso para la construcción de una batería es la extracción de los minerales necesarios, principalmente Litio. En España la primera fábrica de baterías de ion litio estará en Badajoz, para aprovechar la explotación de la mina de litio de Las Navas. No se descarta que Volkswagen quiera colocar su gigafactoría en una ubicación similar.
Tras recoger el litio, el cobalto y otros minerales necesarios, es el momento de la preparación y mezcla del material activo. Con esto se crean los electrodos, separando ánodo y cátodo. Posteriormente es donde se realiza el ensamblaje de las celdas, organizadas en módulos y finalmente en las propias baterías. Las baterías, que suelen funcionar a 400V, conectan en serie más de 100 celdas agrupadas en módulos.
En el centro de pruebas es donde se determina que tanto celdas como módulos y baterías cumplen los requisitos necesarios para su utilización, desde el aspecto térmico hasta de seguridad. En total se realizan unos 6.000 análisis diferentes, explica Werner Tietz, vicepresidente de I+D de Seat.
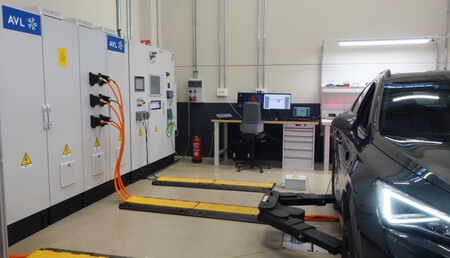
En función de si se trata de una batería de capacidad (para vehículos eléctricos) o una de potencia (para híbridos), las máquinas utilizadas pueden llegar a ser diferentes. Desde Seat explican que trabajan tanto con baterías con una capacidad de 13 kWh, como la del León PHEV, hasta las de 77 kWh, que vemos en el Volkswagen ID.5 y en el futuro Cupra Tavascan.
Según nos explica Francesc Sabate, responsable de desarrollo del Laboratorio de baterías de alta y baja tensión en Seat, la principal diferencia entre las baterías de más o menos capacidad está en la distribución de los módulos y las celdas. En el caso de la de 58 kWh del Cupra Born tenemos 9 módulos y un peso total de 376 kg, donde cada módulo por si solo pesa unos 32 kg. En la de 77 kWh se añaden más módulos y se distribuyen las celdas de manera diferente.
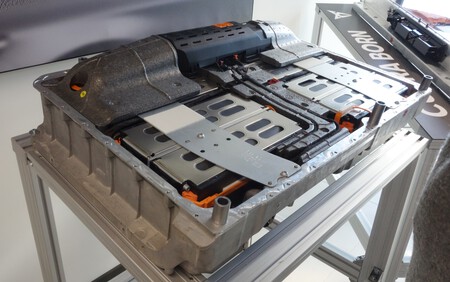
Además de los módulos de celdas, las baterías incorporan otros elementos. Tenemos la tapa superior, que es la que protege el sistema interno y ayuda a dar rigidez estructural a la batería. Contamos con el cableado de comunicación y medida, conectores de los módulos, un controladores de las celdas y los módulos, los propios módulos de celdas, una caja de batería para dar rigidez interna y conectores de conexión entre los módulos de celdas. Finalmente se añade también una placa de refrigeración para compensar el calor generado.
En el caso de las baterías MQB para vehículos eléctricos tenemos una disposición diferente. Ahí se apuesta por tubos de refrigeración y se añade una válvula de compensación de presión. La cantidad de módulos de celdas es considerablemente inferior.
Hasta 6.000 análisis diferentes
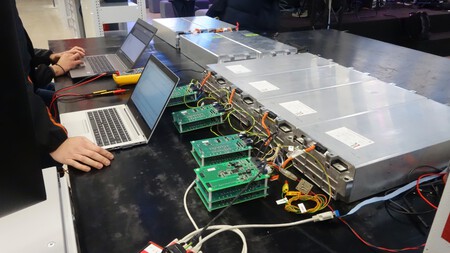
El centro de pruebas de baterías de Seat dispone de una capacidad de ensayo de 1,3 megavatios, una potencia equivalente a tener 100.000 móviles cargando simultáneamente. En las instalaciones se encuentran trabajando 25 técnicos e ingenieros y pudimos observar cómo funcionan las distintas secciones que tienen activas.
El TCE cuenta con una sala de programación, donde se desarrollan algoritmos tanto para testear eventos concretos como para la cámara de visión por computador. De los 6.000 tests, la mitad son de seguridad funcional. Es decir, enfrentar a las baterías a eventos extremos para ver cómo responden. Según describen desde Seat, un coche como el Cupra Born dispone de unos 100 millones de líneas de código.
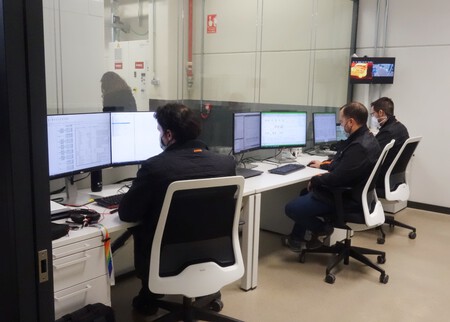
Las baterías se someten a pruebas de validación relacionadas con el sistema de alto voltaje (batería, carga y seguridad) y una de las intenciones es también comprobar que son capaces de rendir durante todo su ciclo de vida. Para ello se someten a una media de 17.500 horas de pruebas. Según Seat, se asegura una vida útil de sus baterías en unos 8 años o unos 160.000 kilómetros, donde pasado ese tiempo mantienen un 70% de la capacidad.
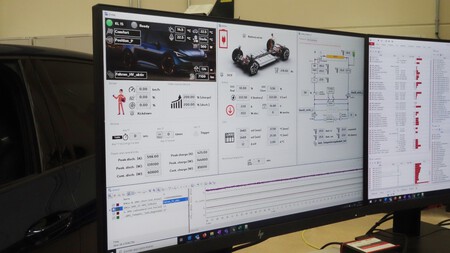
Un gran espacio está ocupado por distintas cámaras climáticas. Disponen de cámaras con una potencia de hasta 300kW para las baterías de coches eléctricos hasta cámaras de 21 kW para las variantes mild-hybrid. Los responsables del centro explican que no solo se realizan pruebas para las baterías de los coches Seat o Cupra, sino que reciben encargos del Grupo Volkswagen para modelos que no se producirán en España.
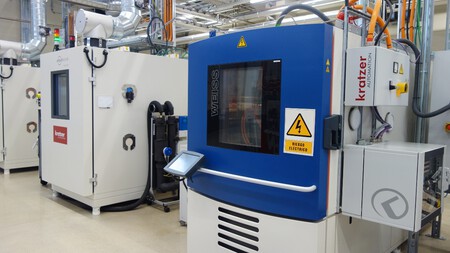
Estas cámaras climáticas cuentan con mecanismos de seguridad como electroválvulas o extracción de gases y permiten comprobar la resistencia térmica de las baterías. Se realizan pruebas entre -25ºC y +55ºC, aunque aseguran que las cámaras están preparadas para alcanzar -55ºC y +120ºC. Las cámaras climáticas del TEC son nuevas, salvo una de ellas que se ha reaprovechado y se ha homologado para poder trabajar con baterías para todo el grupo.
Las baterías suponen entre el 30 y el 40% del coste del coche eléctrico
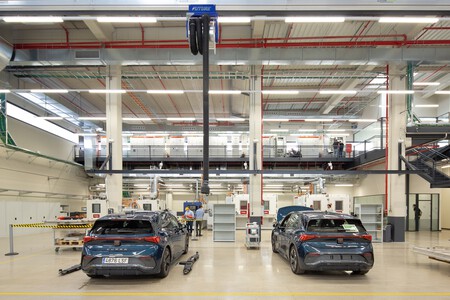
La inauguración del centro de baterías contó con la presencia de Wayne Griffiths, CEO de Seat y Cupra y Diana Morant, ministra de Ciencia. Este proyecto forma parte de la inversión de 5.000 millones de euros que el fabricante alemán realizará en España en su apuesta por electrificar la compañía. Su construcción ha durado un año y medio y empezaron a trabajar después de verano, siendo ahora su apertura oficial.
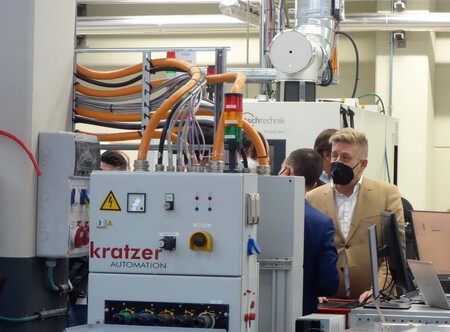
Las baterías suponen uno de los elementos más importantes para el coche eléctrico y apuntan que estas acaban representando entre el 30 y el 40% del coste del vehículo. El centro cuenta también con un taller diseñado para realizar test en vehículos electrificados, pudiendo probar hasta 8 coches a la vez. Aquí es donde se hacen pruebas de energía, seguridad funcional y la integración de las funciones con la electrónica del coche, para por ejemplo si hay una sobrerecarga se muestra una advertencia al conductor.
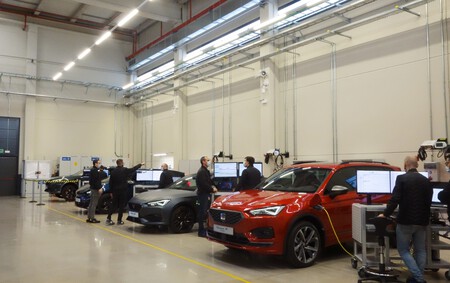
A la hora de realizar las pruebas vemos a distintos vehículos de Seat y Cupra conectados a centralitas que permiten realizar pruebas de diagnóstico. Desde la compañía explican que se han programado interfaces personalizadas para visualizar de forma rápida algunos datos.
También cuentan con cámaras de visión por computador instaladas en el interior del vehículo que les permiten apuntar a las pantallas que ve el conductor y así ir comprobando si aparecen los respectivos símbolos y avisos relacionados con las baterías. Los técnicos someten al coche y su batería a distintas situaciones y ven cómo responde el vehículo.
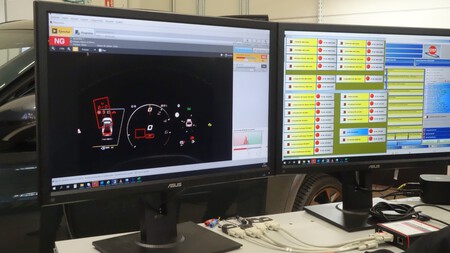
El centro cuenta con un almacén de baterías de alta tensión y un espacio de "innovación abierta", referido a unas oficinas donde permiten que universidades y empresas externas se establezcan y aprovechen la maquinaria del centro de pruebas para sus estudios y proyectos.
Además de coches eléctricos e híbridos, el centro de pruebas de baterías también se utiliza para los motocicletas y patinetes eléctricos de Seat, de la serie MÓ.
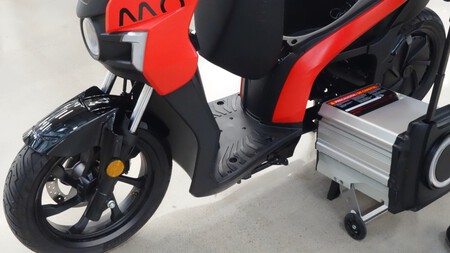
En el exterior del edificio disponen de seis puntos de recarga para comprobar funciones de bidireccionalidad y que la recarga se realiza correctamente. El equipo de Seat explica que tienen previsto instalar un punto de recarga de 350 kW antes de final de año. Una recarga rápida que es el santo grial de los coches eléctricos y donde en este centro de pruebas también tendrán la responsabilidad de comprobar que funciona como es debido.
Ver 32 comentarios