Los cambios que viene propiciando la incorporación de internet y las TIC a nuestro día a día van más allá de los usos con los que ya estamos más familiarizados. En la era de eso que denominamos internet de las cosas, las fábricas del futuro también se van a beneficiar de esa conectividad. No hablamos de un horizonte muy lejano: los cambios ya han comenzado a tomar forma.
De la misma manera que la máquina de vapor, la electricidad y la electrónica estuvieron detrás de las primeras tres revoluciones industriales, hoy asistimos a una nueva revolución que tiene mucho que ver con la manera en que la internet de las cosas va a servir como soporte fundamental para los nuevos tiempos industriales que se avecinan.
¿Cómo serán más competitivas las fábricas del futuro?
La IV Revolución Industrial se apoya en esa práctica instantaneidad que ya vemos como normal en nuestras comunicaciones y en la manera que tenemos de informarnos de cuanto ocurre en el mundo. De una forma análoga, la nueva industria reconvertida tras esta IV Revolución se beneficia de la transmisión de datos en tiempo (casi) real y de la integración de las TIC en todos los procesos de la producción. Además, en España son el principal generador de empleo cualificado y de I+D+i.
Diseño, planificación, ingeniería y desarrollo, puesta en marcha de la producción, comercialización y mantenimiento de un producto son etapas en las que un nuevo software concebido para aprovechar esta revolución tecnológica mejora la automatización de procesos hasta el punto de poder dar una mayor personalización del producto que se fabrica en serie sin perder la necesaria competitividad, lo que es una estrategia básica hoy por hoy.
Pensemos por un momento en la última revolución industrial que conocimos, cuando muchos mecanismos pasaron a ser gestionados de forma electrónica. El salto en competitividad fue enorme, ya que la electrónica introdujo una nueva dimensión en los flujos de trabajo: los intervalos se redujeron en cada ciclo de forma inusitada y las producciones aumentaron de manera espectacular. Y lo hicieron con un coste económico cada vez menor, lo que permitió la popularización de una cantidad inmensa de productos que se denominó muy acertadamente electrónica de consumo.
De una forma muy parecida, la automatización de procesos y el control telemático de cada punto de la cadena de producción llevan aparejada una reducción de los tiempos y una reducción de costes que son beneficiosas para la fábrica y para los consumidores del producto. Pero no sólo eso: la digitalización, la unión de la automatización con el uso de las TIC, permite un mayor margen de maniobra ante posibles imprevistos.
La detección del imprevisto en el menor tiempo posible es una ventaja que permite dar una respuesta cuanto antes. Por ejemplo, si a un operario le deja de funcionar una máquina, el aviso es inmediato, la reposición o reparación de la máquina también comienza en el mismo momento, incluso se puede redistribuir la producción entre otras líneas y, por fin, se puede llevar una estadística fiable de cuál ha sido el impacto de las averías de ese tipo de máquina a lo largo del tiempo.
De hecho, hasta los imprevistos se pueden poner a prueba con la ayuda de las tecnologías que van a cambiar para siempre nuestra concepción de la industria. Y esto se refiere tanto a los imprevistos de una producción tipo (rotura de stocks en el proveedor, error de recuento en la línea de producción, problemas en las expediciones) como al más indeseado de los imprevistos: el accidente laboral.
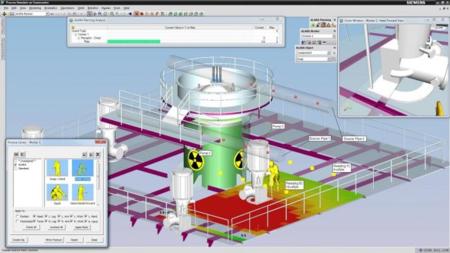
Pongamos que necesitamos ver cuáles son los riesgos laborales de un trabajador en un espacio concreto. Recreando el puesto de trabajo dentro de su escenario, es posible realizar prevención de riesgos laborales en el sentido más etimológico de la expresión. Con una herramienta como el PLM de Siemens, es posible prever los riesgos en un simulador 3D y así aplicar las soluciones más beneficiosas para el trabajador y la empresa sin necesidad de esperar a que ocurra el accidente.
Hablamos de un futuro que ya es presente. Tanto en Europa como en Estados Unidos ya hay empresas que utilizan este tipo de software para simular situaciones comunes en las fábricas. Donde hay un riesgo, hay un avatar de un trabajador dispuesto a experimentar lo que le podría suceder a ese trabajador, pero sin exponer al riesgo a ningún ser de carne y hueso. ¿Algunos ejemplos? La automovilística Ford y la NASA son dos nombres que ya aprovechan estas posibilidades y lo hacen de manera exitosa.
Prototipos virtuales que mejoran la salud
Jack y Jill son los avatares de Siemens. Tienen 68 articulaciones, pueden realizar 135 movimientos y poseen una constitución muy similar a la de los trabajadores de la fábrica. En cada zona del mundo donde se utilizan, Jack y Jill adoptan la morfología de los habitantes del lugar, y es que por lo general no es igual de alto un hombre chino que uno norteamericano. Las consecuencias derivadas de un siniestro laboral tampoco pueden ser las mismas.
Los avatares aprenden los movimientos reales de las personas gracias a Microsoft Kinect. Cuando ya están registrados, estos movimientos se procesan hasta encontrar puntos críticos en las labores habituales de los trabajadores. Por ejemplo, es posible recrear la fatiga que sufrirá un trabajador manejando material pesado. De esta manera se puede mejorar la actividad productiva desde el punto de vista de la salud laboral sin necesidad de fabricar caros prototipos para ensayar la producción una y otra vez.
Además, al poder experimentar desde el comienzo del desarrollo del producto, es posible optimizar la producción de forma que se evitan errores de diseño. Esto tiene otra consecuencia positiva, y es que los productos ganan en seguridad y en calidad.
¿Qué recorrido tienen por delante las fábricas del futuro?
La incorporación de las innovaciones tecnológicas que son el punto esencial de las fábricas del futuro supone un antes y un después en la industria. Este punto de inflexión se materializa no sólo en cambios internos de las plantas de producción, sino también en el día a día de los trabajadores.
Atrás quedó aquel obrero vestido con mono azul que fue la imagen clásica de las fábricas del siglo XX. El trabajador de las fábricas del futuro es un profesional altamente capacitado que ya no se encuentra siempre en un mismo punto de la producción, sino que se conecta a la red y trabaja sin problemas en una u otra ubicación, porque conoce todos los puestos de trabajo de la planta, mientras que son los robots los que garantizan una producción rápida y eficiente lo que se traduce en un mejor aprovechamiento de los recursos, incluidos los energéticos.
Este es el futuro de las fábricas, y este futuro se enmarca en un mundo globalizado. Si antes de este escenario ser competitivo era importante, con un mercado mundial único ser competitivo es una necesidad vital. La digitalización entendida como la automatización de procesos y el máximo aprovechamiento de las tecnologías asociadas a la IV Revolución Industrial son el camino para conseguir producir más, de forma personalizada, en intervalos cortos, con calidad y con eficiencia.
Ver 5 comentarios